Jul 17, 2009
Design and Fabrication of IC Engine Powered Radio Control Car
Guest article by Srihari.B
The Radio control dates back to the nineties when it first evolved. It is a hobby for most of the engineering and automobile enthusiasts. It is proved by its rigidity, precision and ability.
The design of such RC cars has become a great market in the western nations. The design of such RC car involves precision, rigidity and team work too
This project involves the design of the chassis and steering system of a 3cc IC engine powered radio control car and to match its performance with that of the originally available components.
The main objectives of this project are
A radio-controlled car (R/C car) is a powered model car driven from a distance using a radio control system. Inputs from joysticks (or a wheel and a trigger) on a transmitter are sent to the car's onboard receiver. The receiver interprets the radio signals and sends electrical pulses to the servo and electronic speed controller, making the model turn its wheels and the motor run.
Cars are powered by various sources. Electric cars are powered by small but powerful electric motors and rechargeable nickel-cadmium, nickel metal hydride, or lithium polymer cells. There are also brushed or brushless electric motors. Most fuel-powered models use glow plug engines, small internal combustion engines fueled by a special mixture of nitro methane, methanol, and oil (in most cases a blend of castor oil and synthetic oil). These are referred to as "nitro" cars.
Further these cars can be classified as Off-road and on-road models. Off-road models, which are built with fully-functional off-road suspensions, can be used on various types of terrain. In comparison, on-road cars, which generally have a limited or non-existent suspension, are strictly limited to smooth, paved surfaces
1.2 IC Engine Powered Car:
An R/C car can be powered by motors or engines. The cars that are powered with engines are called as Nitro-powered RC car. They use methanol as a basic fuel with a percentage of nitro methane as booster and castor oil for lubrication.
Fuel-powered engines allow model cars to reach moderate speeds unmodified. Maximum power is generally achieved at medium to high speeds and a slightly slower throttle response than electrically powered vehicles are to be expected. Electric motors effectively produce instantaneous torque, where nitro engines, like full-sized gasoline engines, take time for the engine to spool up and for the clutch to engage. Nitro- (and fuel) powered cars may be refueled and returned to action in a few seconds, as opposed to electrics needing to remove the body shell and battery fasteners to replace a discharged battery. Nitro cars are completely air cooled, and may be run continuously with no need to take breaks for cooling down. Nitro cars tend to be larger than electric cars on average
1.3 Principle of Operation:
Radio-controlled cars use a common set of components for their control and operation. All cars require a transmitter, which has the joysticks for control, or in pistol grip form, a trigger for throttle and a wheel for turning, and a receiver which sits inside the car. The receiver changes the radio signal broadcast from the transmitter into suitable electrical control signals for the other components of the control system. Most radio systems utilize amplitude modulation for the radio signal and encode the control positions with pulse width modulation. Upgraded radio systems are available that use the more robust frequency modulation and pulse code modulation. The radio is wired up to either electronic speed controls or servomechanisms which perform actions such as throttle control, braking, steering, and on some cars, engaging either forward or reverse gears. Electronic speed controls and servos are commanded by the receiver through pulse width modulation; pulse duration sets either the amount of current that an electronic speed control allows to flow into the electric motor or sets the angle of the servo. On the models the servo is attached to at least the steering mechanism; rotation of the servo is mechanically changed into a force which steers the wheels on the model, generally through adjustable turnbuckle linkages. Servo savers are integrated into all steering linkages and some nitro throttle linkages. A servo saver is a flexible link between the servo and its linkage that protects the servo's internal gears from damage during impacts or stress.
The whole machine is divided into three major categories:
1) Engine
2) Chassis and Suspension
3) Control
2. Engine
2.1 Introduction

2.2 Glow plugs

To start a glow plug engine, a small direct current (around 1.5 volts) is applied to the glow plug, initially heating the filament. The engine is then spun from the outside to introduce fuel to the chamber. Once the fuel has ignited and the engine is running, the electrical connection is removed. Each combustion keeps the plug's filament glowing hot, allowing it to ignite the next charge, thus sustaining the power cycle.
Technically a glow plug engine is similar to a diesel engine in that it uses internal heat to ignite the fuel, but since the ignition timing is not controlled by fuel injection (as in an ordinary diesel), or electrically (as in a spark ignition engine), it must be adjusted by changing fuel/air mixture and plug/coil design. A richer mixture will tend to cool the filament and so retard ignition, slowing the engine. This "configuration" can also be adjusted by using varying plug designs for a more exact thermal control.
2.3 Fuel
Glow engines cannot be operated with the same gasoline you get at a filling station pump. They require a special fuel, called “glow fuel”. It contains methanol as the base, with varying amounts of nitro methane to increase the energy that the fuel can provide. Oil, pre-mixed into the fuel, lubricates and protects the tiny engine as it pounds out amazing power. The mixture of the fuel is 85% methanol and 15% castor oil.
2.4 Carburetor
3. Chassis & Suspensions:
The chassis should be light in weight, strong and also able to accommodate all the components. It can be made of aluminum or carbon graphite. The chassis should bear the whole weight of the car. So it should be rigid and also accommodate the other forces acting on it.
The basic components of a car are
1) a) Rear drive shaft or dog bone b) Front dog bone
2) Front and rear disk brakes.
3) Center bulkhead.
4) Fuel tank
5) Center differential and spur gear.
6) a) Rear chassis brace
b) Front chassis brace
7) Servo tray
8) Battery and receiver box
9) Rear shock tower. The shock tower has many different mounting holes for both the shock and camber link.
10) Rear camber link – turnbuckle (adjustable)
11) Rear hub carrier.
12) Rear suspension arm.
13) Rear sway bar.
14) Rear CVD shaft.
15) Rear hub.
16) Rear differential housing, differential and rear bulk head.
17) Rear springs.
18) Rear shocks


20) Front CVD
21) Front lower suspension arm
22) Upper suspension arm - A-arm.
23) Front shock tower.
24) Front drive shaft or dog bone.
25) Steering knuckle.
26) Front hub.
27) Front sway bar.
28) Front differential, differential housing and bulkhead.
3.1 Suspensions
The main component of a suspension is its springs. Coil springs are used commonly. These are usually placed around the damper housing to form a spring-damper unit. A spring is an elastic device that resists movement in its direction of work
The main job of the suspension system is the following,
This refers to the clearance between the ground and the chassis, both at the front and the back of the vehicle. The spring adjusters on the shock can be adjusted (which are at the top of each shock spring) until the appropriate height is achieved after the drop test. If you have an on-road vehicle, you should place it on a flat hard surface, compress the suspension a few times by pressing on the chassis and let it return to its normal position
It is the angle of the front tires when viewed from above when the suspension arms are level. If the fronts of the tires angle in, it is called “toe-in” and if the fronts of the tires angle out, it is called "toe-out.” This is adjusted by turning the steering rods - the rods that run between the front hub and the steering linkage that is mounted on the chassis.
3.1.3 Camber
Camber is the angle of the tops of the tires when viewed from the front. Negative camber is when the tops of the tires are angled towards the center of the vehicle. Positive camber is where the tops of the tires are angled away from the center of the vehicle. Positive camber is very rarely used, if ever. A small amount of rear negative camber is helpful to increase traction in the rear. Negative camber at the front will increase stability.
4. CHASSIS FABRICATION
4.1 Fabricated chassis
The chassis has very minimal flex and is very rigid. The chassis is hand worked in a tincture shop and all the holes and the spur clearance and starter box provisions are drilled to match with the required dimension to suit the layout of the car.
The following alterations are made on the new chassis:
Ø Added material for extra strength at the corners
Ø Bent sides which will act as a bumper in one way and also reduces the longitudinal torsion
4.2 Method of Fabrication:
The raw material taken was Aluminium 6061 and of thickness 3mm.
Then the various processes that were done on the sheet were
5. STEERING MECHANISMS:
The steering mechanism of this on-road vehicle is totally unique where we have eliminated all the ball and socket joints in order to make the mechanism as well as the fabrication part a bit simpler.
5.1 Steering Link Design
The objective of the design was to eliminate the ball and socket joint. So the single member was split into three different components. The one was a rod with external threads. The other member is to hold the joint and the third member will have one rotational degree of freedom.


5.2 Steering Link Assembly
It bears some similarity with a universal joint but how ever the application part is new!!! The brown member is a stud on which two brackets are screwed into. Then the green member is a ‘free to oscillate’ kind of member which will effectively allow both the degrees of freedom that a ball and socket joint would do.





DISPLACEMENT: .183ci (3.008cc)
BHP: 2.27 at 31,761 rpm
TORQUE: 84.58 in.-oz. at 24,000 rpm
BORE: .629 in. (15.97mm)
STROKE: .590 in. (14.986mm)
PORTS: 5-port
Practical rpm: 3,000-34,000
CRANKSHAFT O.D.: .471 in. (11.963mm)
CRANKSHAFT I.D.: 305 in. (7.747mm)
CRANKSHAFT PIN: .175 in. (4.445mm)
PIPE: X12 Turbo
PLUG: O.S. Turbo P3
ENGINE TEMP: 230°F
EGT: 625°F
HEAD SHIMS: (1) .007 in., (1) .0035 in.
HEAD VOLUME: .21cc
POWER STROKE: .370 in. (9.398mm)
COMPRESSION RATIO(S): Trapped 7.89:1 Geometric 11.99:1
INDUCTION DURATION: 208 degrees
EXHAUST DURATION: 164 degrees
TRANSFER DURATION: 124 degrees
BOOST DURATION: 108 degrees
6.2 Port Configurations:
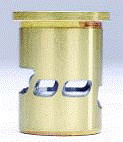
6.3 Dyno Tests:
Red Line: Peak Bhp 2.28 @ 30500 RPM
6.4 Advantages:
Oversize fins on the case dissipate heat to help keep engine temperatures lower.
Five ports in the liner increase air flow for more power.
The rear bearing is 12 mm in diameter, which lessens vibration and allows the engine to handle more torque.
A super-hot turbo P3 plug is included for better burn, more power and improved fuel economy.
The 18TZ-TX version features a new compact recoil starter that's smaller and lighter, making it easier to install.
7. Basic Components - Specifications:
Length: 431mm
End to end width: 310mm
Distance between wheel centers: 325mm
Ground clearance: 25mm
Diameter of wheel: 100mm
7.1 MECHANICAL COMPONENTS:
The following components are classified under the mechanical components,

7.1.2 Clutch

7.1.3 Gear box:

Brake: Disc type
Material: Fiber glass
7.1.4 Differential with casing

7.1.5 Suspension system:
The suspension system of the RC car is a wish bone type of suspensions with all the upper and lower arms made of plastic. The suspension is again an individual suspension.

Spring material: carbon steel
Free length: 35mm
Pitch: 5mm
No of turns: 7
Damping is provided using the suspension oil.Damping is needed to absorb the energy associated with suspension travel. That suspension travel can be induced by bumps, or lateral or longitudinal acceleration. Without damping, the magnitude of the suspension movement would never stop increasing, leading to a very humorous situation. In terms of energy, damping absorbs most of the energy the car receives as it moves, unlike springs stores the energy, and release it again
7.2 ELECTRICAL & ELECTRONIC COMPONENTS:
The electrical and electronic components basically aids in the control of the steering and the throttle. The electronic components in the RC car are,
1. Crystal Transmitter
2. Battery pack
3. Servo motors
4. Radio Pistol
7.2.1 Crystal transmitter:
The crystal transmitter transmits AM radio waves which is received by the receiver and controls the servo motors. The frequency of the transmitter is 24.045 MHz

1.5 v AA size batteries
7.2.2 Servos

HS311 Servo Specs:
Speed: 0.19 sec/60 degrees at 4.8V
Speed: 0.15 sec/60 degrees at 6.0V
Torque: 42.00 oz-in at 4.8V
Torque: 51.00 oz-in at 6.0V
Length: 1.60" (41mm)
Width: 0.80" (20mm)
Height: 1.40" (37mm)
Weight: 1.5oz (43g)

7.2.3 Radio:

Pistol grip radios contain the transmitter. The trigger is used for the acceleration and braking. The steering is controlled by the steering wheel kind of control. The pistol grip radio is a three way control as it controls acceleration, braking and steering
Pistol grip radio
AM Transmitter/Receiver
27.045MHz band
Output power: <0.75 mW
Current Drain (w/servos): approximately 250mA
BODY
The body of the RC car is important in the way of protecting the engine and other critical parts from damage due to accidents. It will also in some way help in the aerodynamics of the car and it gives aesthetics to the car.
The body of the car is tinkered from a 3mm thick mild steel sheet and is welded to obtain the shape of the sedan.
The shape of the body was achieved by sheet metal working and welding of the ends.
9. Work progress in phases:
10. TEST RESULTS
The results obtained in the fabrication of the RC car can be compared with the actual readymade model and the various deviations and accuracies can be known. The results are tabulated as that of the specifications of a real car.
The following results were obtained during the final testing,
Price - Rs.16,618
Length: 431mm
End to end width: 310mm
Distance between wheel centers: 325mm
Ground clearance: 25mm
Diameter of wheel: 100mm
Turning Circle: 400mm
Kerb Weight: 5 Kgs
Engine: 3cc OS engine
Peak Bhp 2.28 @ 30500 RPM
Peak torque 83.1 oz-in @ 25850 RPM torque—83.1
Steering Type – Bell crank mechanism with universal joints
Suspensions – Double wish bone suspensions
Brake – transmission disc brake
Top Speed – 60 KMPH
Fuel tank capacity – 150 ml
Steering control: High torque Servo motor:
Throttle and braking control: Servo motor
1st Gear engagement: 0-5000 RPM
2nd Gear engagement: 5000-35000 RPM
Braking: 50-0 KMPH in 3 seconds
Acceleration: 0-50 KMPH in 3.5 seconds
Courtesy and References:
The successful completion of this project is a glittering hallmark of academic achievement and I am greatly indebted to scores of individuals who have contributed their mite for the jubilant finish of this project work. I would like to express my sincere thanks to the following people, who in one way or the other helped or inspired me in the success of this project.
Mr.Murarie kumar, Mentor, guide and sponsor of this project
Dr. P.V.Mohanram, Head of Department of Mechanical Engineering
Mr. B.Giriraj, Faculty, Department of Mechanical Engineering
Sowrirajan K, Team member
Rakesh Narayanan, Team member
Ramani S, Team member
Ragunathaprabhu S, Team member
- To design a specific chassis system to accommodate all the components of the RC car to be mounted on to it.
- The design of the steering system which should be capable of steering the car like the already available mechanism and also to eliminate the ball joints present in the steering mechanism.
- To fabricate the suspension arms to improve strength.
- To fabricate a suitable body for the RC car.
A radio-controlled car (R/C car) is a powered model car driven from a distance using a radio control system. Inputs from joysticks (or a wheel and a trigger) on a transmitter are sent to the car's onboard receiver. The receiver interprets the radio signals and sends electrical pulses to the servo and electronic speed controller, making the model turn its wheels and the motor run.
RC Buggy (Scale 1:8)
Radio-controlled (or R/C) cars are usually categorized as either "toy" or "hobby" grade. Remote-controlled vehicles differ from radio-controlled by the presence of a wire cable connecting the transmitter and the car, limiting their movementCars are powered by various sources. Electric cars are powered by small but powerful electric motors and rechargeable nickel-cadmium, nickel metal hydride, or lithium polymer cells. There are also brushed or brushless electric motors. Most fuel-powered models use glow plug engines, small internal combustion engines fueled by a special mixture of nitro methane, methanol, and oil (in most cases a blend of castor oil and synthetic oil). These are referred to as "nitro" cars.
Further these cars can be classified as Off-road and on-road models. Off-road models, which are built with fully-functional off-road suspensions, can be used on various types of terrain. In comparison, on-road cars, which generally have a limited or non-existent suspension, are strictly limited to smooth, paved surfaces
1.2 IC Engine Powered Car:
An R/C car can be powered by motors or engines. The cars that are powered with engines are called as Nitro-powered RC car. They use methanol as a basic fuel with a percentage of nitro methane as booster and castor oil for lubrication.
Fuel-powered engines allow model cars to reach moderate speeds unmodified. Maximum power is generally achieved at medium to high speeds and a slightly slower throttle response than electrically powered vehicles are to be expected. Electric motors effectively produce instantaneous torque, where nitro engines, like full-sized gasoline engines, take time for the engine to spool up and for the clutch to engage. Nitro- (and fuel) powered cars may be refueled and returned to action in a few seconds, as opposed to electrics needing to remove the body shell and battery fasteners to replace a discharged battery. Nitro cars are completely air cooled, and may be run continuously with no need to take breaks for cooling down. Nitro cars tend to be larger than electric cars on average
1.3 Principle of Operation:
Radio-controlled cars use a common set of components for their control and operation. All cars require a transmitter, which has the joysticks for control, or in pistol grip form, a trigger for throttle and a wheel for turning, and a receiver which sits inside the car. The receiver changes the radio signal broadcast from the transmitter into suitable electrical control signals for the other components of the control system. Most radio systems utilize amplitude modulation for the radio signal and encode the control positions with pulse width modulation. Upgraded radio systems are available that use the more robust frequency modulation and pulse code modulation. The radio is wired up to either electronic speed controls or servomechanisms which perform actions such as throttle control, braking, steering, and on some cars, engaging either forward or reverse gears. Electronic speed controls and servos are commanded by the receiver through pulse width modulation; pulse duration sets either the amount of current that an electronic speed control allows to flow into the electric motor or sets the angle of the servo. On the models the servo is attached to at least the steering mechanism; rotation of the servo is mechanically changed into a force which steers the wheels on the model, generally through adjustable turnbuckle linkages. Servo savers are integrated into all steering linkages and some nitro throttle linkages. A servo saver is a flexible link between the servo and its linkage that protects the servo's internal gears from damage during impacts or stress.
Belt Driven On-road Car (Scale 1:10)
Fuel powered models utilize a servo for throttle and braking control; rotation of the servo in one direction will cause the throttle on the carburetor to open, providing more air and fuel mixture to the internal combustion engine. Rotation of the servo in the other direction causes torque to be applied to a piece which causes friction with the braking material. The brake is located on the driveshaft and stops only two wheels on a two-wheel drive car and all four wheels on a four-wheel drive car.The whole machine is divided into three major categories:
1) Engine
2) Chassis and Suspension
3) Control
2. Engine
2.1 Introduction
Engine
Most gas R/C models use a 2- or 4-stroke glow engine, sized specifically for that model. Glow engines have a simple ignition system that uses a glow plug rather than a spark plug so there’s no coil, magneto or points. The glow plug is heated by a battery-operated glow starter. When fuel enters the combustion chamber, it’s ignited by the heated glow plug and with that, the engine springs to life, instantly gaining the momentum to continue running after all the starter accessories are removed. The engine’s carburetor supplies the fuel and air needed for combustion. It has several adjustments. A rotating throttle arm controls the amount of fuel and air that enters the combustion chamber. The high-speed needle valve controls the mix or proportions of fuel vs. air at mid- to high-speeds. The idle mixture screw is similar to the high-speed needle valve, except that it controls the mix of fuel and air when the engine is only idling. 2.2 Glow plugs
Glow plugs
A gasoline combustion engine uses a spark plug to ignite the fuel-air mixture within the compression chamber, so a glow or nitro engine uses a small glow plug. Although the plug needs to be heated up using a glow plug igniter initially, once the engine is running, the heat generated within the combustion chamber keeps the plug glowing constantly and is thus able to ignite the fuel-air mixture on each revolution. To start a glow plug engine, a small direct current (around 1.5 volts) is applied to the glow plug, initially heating the filament. The engine is then spun from the outside to introduce fuel to the chamber. Once the fuel has ignited and the engine is running, the electrical connection is removed. Each combustion keeps the plug's filament glowing hot, allowing it to ignite the next charge, thus sustaining the power cycle.
Technically a glow plug engine is similar to a diesel engine in that it uses internal heat to ignite the fuel, but since the ignition timing is not controlled by fuel injection (as in an ordinary diesel), or electrically (as in a spark ignition engine), it must be adjusted by changing fuel/air mixture and plug/coil design. A richer mixture will tend to cool the filament and so retard ignition, slowing the engine. This "configuration" can also be adjusted by using varying plug designs for a more exact thermal control.
2.3 Fuel
Glow engines cannot be operated with the same gasoline you get at a filling station pump. They require a special fuel, called “glow fuel”. It contains methanol as the base, with varying amounts of nitro methane to increase the energy that the fuel can provide. Oil, pre-mixed into the fuel, lubricates and protects the tiny engine as it pounds out amazing power. The mixture of the fuel is 85% methanol and 15% castor oil.
2.4 Carburetor
Carburetor
Sitting at the front of the engine on top of the crankshaft is the carburetor, which is the part of the engine that introduces the fuel into the crankcase. The fuel / air mixture is ignited by a glow plug which is screwed into the top of the cylinder head.3. Chassis & Suspensions:
The chassis should be light in weight, strong and also able to accommodate all the components. It can be made of aluminum or carbon graphite. The chassis should bear the whole weight of the car. So it should be rigid and also accommodate the other forces acting on it.
The basic components of a car are
1) a) Rear drive shaft or dog bone b) Front dog bone
2) Front and rear disk brakes.
3) Center bulkhead.
4) Fuel tank
5) Center differential and spur gear.
6) a) Rear chassis brace
b) Front chassis brace
7) Servo tray
8) Battery and receiver box
9) Rear shock tower. The shock tower has many different mounting holes for both the shock and camber link.
10) Rear camber link – turnbuckle (adjustable)
11) Rear hub carrier.
12) Rear suspension arm.
13) Rear sway bar.
14) Rear CVD shaft.
15) Rear hub.
16) Rear differential housing, differential and rear bulk head.
17) Rear springs.
18) Rear shocks
Rear suspensions
Front steering and suspensions
19) Upper and lower pivot/pillow balls. They thread into both the upper and lower A-arms. This gives you the ability to change camber. 20) Front CVD
21) Front lower suspension arm
22) Upper suspension arm - A-arm.
23) Front shock tower.
24) Front drive shaft or dog bone.
25) Steering knuckle.
26) Front hub.
27) Front sway bar.
28) Front differential, differential housing and bulkhead.
3.1 Suspensions
The main component of a suspension is its springs. Coil springs are used commonly. These are usually placed around the damper housing to form a spring-damper unit. A spring is an elastic device that resists movement in its direction of work
The main job of the suspension system is the following,
- Maintain the ride height
- To provide damping
- To give the best suspension travel for a typical car
- To prevent the car from rolling
- To protect the car and all its components
This refers to the clearance between the ground and the chassis, both at the front and the back of the vehicle. The spring adjusters on the shock can be adjusted (which are at the top of each shock spring) until the appropriate height is achieved after the drop test. If you have an on-road vehicle, you should place it on a flat hard surface, compress the suspension a few times by pressing on the chassis and let it return to its normal position
Deflection of different springs
3.1.2 Toe-In/Toe-OutIt is the angle of the front tires when viewed from above when the suspension arms are level. If the fronts of the tires angle in, it is called “toe-in” and if the fronts of the tires angle out, it is called "toe-out.” This is adjusted by turning the steering rods - the rods that run between the front hub and the steering linkage that is mounted on the chassis.
3.1.3 Camber
Camber is the angle of the tops of the tires when viewed from the front. Negative camber is when the tops of the tires are angled towards the center of the vehicle. Positive camber is where the tops of the tires are angled away from the center of the vehicle. Positive camber is very rarely used, if ever. A small amount of rear negative camber is helpful to increase traction in the rear. Negative camber at the front will increase stability.
4. CHASSIS FABRICATION
Comparison with Fabricated Chassis (Left - Modified Chassis, Right - Original Chassis)
4.1 Fabricated chassis
The chassis has very minimal flex and is very rigid. The chassis is hand worked in a tincture shop and all the holes and the spur clearance and starter box provisions are drilled to match with the required dimension to suit the layout of the car.
The following alterations are made on the new chassis:
Ø Added material for extra strength at the corners
Ø Bent sides which will act as a bumper in one way and also reduces the longitudinal torsion
Specifications | Fabricated Chassis | Readymade Chassis |
Material Thickness Mass Length Width Maximum thickness | Aluminum 6061 3mm 750gms 392mm 225mm 12.2mm | Carbon Graphite 2mm 500gms 392mm 190mm 7mm |
Table 4.1 Comparison between the fabricated and readymade chassis
4.2 Method of Fabrication:
The raw material taken was Aluminium 6061 and of thickness 3mm.
Then the various processes that were done on the sheet were
- Cutting and parting off : The chassis was cut to the required dimension with the help of the readymade chassis
- Drilling: The required holes for the mounting of the various components were measured and then drilled on to the chassis
- Slot Drilling: The slots for the flywheel for starting and stopping the engine are also provided. It was machined using a hand drill
- The corner bends were provided in order to prevent the flexing and bending of the member
- The slots were also given for the mounting of the servo motors in position.
5. STEERING MECHANISMS:
The steering mechanism of this on-road vehicle is totally unique where we have eliminated all the ball and socket joints in order to make the mechanism as well as the fabrication part a bit simpler.
Drag links with ball and socket joints
The challenge here was to eliminate all the joints with two or more degree of freedoms and restrict it to one degree of freedom in two directions. The idea was inspired from the universal joint. Usually the joints are made of plastics. The material selection was also a challenging task since it has to have the strength and functionality as that of the readymade one. 5.1 Steering Link Design
The objective of the design was to eliminate the ball and socket joint. So the single member was split into three different components. The one was a rod with external threads. The other member is to hold the joint and the third member will have one rotational degree of freedom.
Steering Components
Stud
The component in Fig 5.1 is fastened with the stud and on the other end is a freely rotating member which will be fastened with the hub on one end and to the servo link on the other end. It will provide the two DOF and also is easy to fabricate. 5.2 Steering Link Assembly
It bears some similarity with a universal joint but how ever the application part is new!!! The brown member is a stud on which two brackets are screwed into. Then the green member is a ‘free to oscillate’ kind of member which will effectively allow both the degrees of freedom that a ball and socket joint would do.
Steering Mechanism Assembly
For example the member on the left is oscillating along the XX axis then the member on the right will oscillate along the YY axis thus satisfying the conditions of a steering link. Steering links
The links shown here will be substituted instead of the ball and socket joints. The small member is the member that will move both in X and Y directions and the bigger member is the coupling member.Steering Link in the car
6. ENGINE: O.S. 18 TZ (S)-TOS ENGINE
6.1 Specifications: DISPLACEMENT: .183ci (3.008cc)
BHP: 2.27 at 31,761 rpm
TORQUE: 84.58 in.-oz. at 24,000 rpm
BORE: .629 in. (15.97mm)
STROKE: .590 in. (14.986mm)
PORTS: 5-port
Practical rpm: 3,000-34,000
CRANKSHAFT O.D.: .471 in. (11.963mm)
CRANKSHAFT I.D.: 305 in. (7.747mm)
CRANKSHAFT PIN: .175 in. (4.445mm)
PIPE: X12 Turbo
PLUG: O.S. Turbo P3
ENGINE TEMP: 230°F
EGT: 625°F
HEAD SHIMS: (1) .007 in., (1) .0035 in.
HEAD VOLUME: .21cc
POWER STROKE: .370 in. (9.398mm)
COMPRESSION RATIO(S): Trapped 7.89:1 Geometric 11.99:1
INDUCTION DURATION: 208 degrees
EXHAUST DURATION: 164 degrees
TRANSFER DURATION: 124 degrees
BOOST DURATION: 108 degrees
6.2 Port Configurations:
0 degree, 90 degree, 180 degree, 270 degree Port Configurations
The exhaust port is widest at the top to allow more exhaust gases to escape quickly. The port in the sleeve very closely matches the shape and position of the exhaust port in the engine block, and that allows exhaust to flow much more smoothly. The Schnuerle ports are two separate ports on each side of the cylinder, and there’s a vane cast into the transfer passage in the block that matches the ports. A single boost port features moderate port timing.6.3 Dyno Tests:
Dyno test
Green Line: Peak torque 83.1 oz-in @ 25850 RPM torque—83.1 oz.-in.Red Line: Peak Bhp 2.28 @ 30500 RPM
6.4 Advantages:
Oversize fins on the case dissipate heat to help keep engine temperatures lower.
Five ports in the liner increase air flow for more power.
The rear bearing is 12 mm in diameter, which lessens vibration and allows the engine to handle more torque.
A super-hot turbo P3 plug is included for better burn, more power and improved fuel economy.
The 18TZ-TX version features a new compact recoil starter that's smaller and lighter, making it easier to install.
7. Basic Components - Specifications:
Basic layout
Length: 431mm
End to end width: 310mm
Distance between wheel centers: 325mm
Ground clearance: 25mm
Diameter of wheel: 100mm
7.1 MECHANICAL COMPONENTS:
The following components are classified under the mechanical components,
- Chassis
- Engine 3.0 cc (0.18TZ OS)
- Air Filter
- Exhaust manifold
- Muffler
- Clutch
- Gear Box
- Differentials
- Front & rear hubs
- Drive Shafts
- Steering System
- Disc Brake
- Front & Rear – Lower & Upper Arms
- Shock Absorbers
- Fuel Tank (150ml)
Exhaust muffler with the engine
The exhaust muffler is an attachment along with the engine. It is tuned in such a way as to reduce the exhaust pressure and hence the noise of the engine to its minimum.7.1.2 Clutch
Centrifugal clutch
The centrifugal clutch is an automatic clutch. The spring tension determines is engagement and disengagement. The clutch engages at 2000- 3000 RPM. The material it is made of is an alloy of brass, so that it can withstand high temperatures and also it has a good coefficient of friction also. The flywheel is a solid aluminium block to store energy during the non-power strokes. 7.1.3 Gear box:
Gear box assembly
- The gear is made of Nylon material
- It is mounted at the center of the chassis and gives power to the two drives that goes to the front and the rear wheels
- It has a gear ratio of 1:2.4 and 1:1.5
Brake: Disc type
Material: Fiber glass
7.1.4 Differential with casing
Differential and casing
The RC car is a four wheel drive with a central drive and two differentials on both the sets of wheels. The material of the bevels used in the differential is a heat treated steel. The basic function of the differential is to control the speed of the wheels rotation while encountering a turn. The differential is lubricated with crease and it is sealed with a plastic casing. The drive shaft is a dog bone shaft and is connected with the differentials using a CV joint. From the differentials the power is transmitted to the wheels using the dog bone shafts.7.1.5 Suspension system:
The suspension system of the RC car is a wish bone type of suspensions with all the upper and lower arms made of plastic. The suspension is again an individual suspension.
Suspension components
Spring type oil damped Spring material: carbon steel
Free length: 35mm
Pitch: 5mm
No of turns: 7
Damping is provided using the suspension oil.Damping is needed to absorb the energy associated with suspension travel. That suspension travel can be induced by bumps, or lateral or longitudinal acceleration. Without damping, the magnitude of the suspension movement would never stop increasing, leading to a very humorous situation. In terms of energy, damping absorbs most of the energy the car receives as it moves, unlike springs stores the energy, and release it again
7.2 ELECTRICAL & ELECTRONIC COMPONENTS:
The electrical and electronic components basically aids in the control of the steering and the throttle. The electronic components in the RC car are,
1. Crystal Transmitter
2. Battery pack
3. Servo motors
4. Radio Pistol
7.2.1 Crystal transmitter:
The crystal transmitter transmits AM radio waves which is received by the receiver and controls the servo motors. The frequency of the transmitter is 24.045 MHz
Transmitter
Battery pack for the radio box (4 numbers) 1.5 v AA size batteries
7.2.2 Servos
Servomotors
One for the steering and the other for throttle and breaksHS311 Servo Specs:
Speed: 0.19 sec/60 degrees at 4.8V
Speed: 0.15 sec/60 degrees at 6.0V
Torque: 42.00 oz-in at 4.8V
Torque: 51.00 oz-in at 6.0V
Length: 1.60" (41mm)
Width: 0.80" (20mm)
Height: 1.40" (37mm)
Weight: 1.5oz (43g)
Servo motor
7.2.3 Radio:
Pistol radio controller
Pistol grip radios contain the transmitter. The trigger is used for the acceleration and braking. The steering is controlled by the steering wheel kind of control. The pistol grip radio is a three way control as it controls acceleration, braking and steering
Pistol grip radio
AM Transmitter/Receiver
27.045MHz band
Output power: <0.75 mW
Current Drain (w/servos): approximately 250mA
BODY
The body of the RC car is important in the way of protecting the engine and other critical parts from damage due to accidents. It will also in some way help in the aerodynamics of the car and it gives aesthetics to the car.
The body of the car is tinkered from a 3mm thick mild steel sheet and is welded to obtain the shape of the sedan.
The shape of the body was achieved by sheet metal working and welding of the ends.
9. Work progress in phases:
Phase -1 Body fabrication, Welding, Painting
Phase -2 Basic work, Chassis modification, Parts matching, Suspension mounting
Phase -3 Engine mounting, Engine assembly, Engine alignment, Final testing
10. TEST RESULTS
The results obtained in the fabrication of the RC car can be compared with the actual readymade model and the various deviations and accuracies can be known. The results are tabulated as that of the specifications of a real car.
The following results were obtained during the final testing,
Price - Rs.16,618
Length: 431mm
End to end width: 310mm
Distance between wheel centers: 325mm
Ground clearance: 25mm
Diameter of wheel: 100mm
Turning Circle: 400mm
Kerb Weight: 5 Kgs
Engine: 3cc OS engine
Peak Bhp 2.28 @ 30500 RPM
Peak torque 83.1 oz-in @ 25850 RPM torque—83.1
Steering Type – Bell crank mechanism with universal joints
Suspensions – Double wish bone suspensions
Brake – transmission disc brake
Top Speed – 60 KMPH
Fuel tank capacity – 150 ml
Steering control: High torque Servo motor:
Throttle and braking control: Servo motor
1st Gear engagement: 0-5000 RPM
2nd Gear engagement: 5000-35000 RPM
Braking: 50-0 KMPH in 3 seconds
Acceleration: 0-50 KMPH in 3.5 seconds
Courtesy and References:
- Mr. Murarie Kumar. Personal and professional support
- OS 18 TZ Engine manual
- www.towerhobbies.com
- http://www.rc-truckncar-tuning.com/RC-Nitro-Engine-Carburetor.html
- http://www.raptortechnique.com/enginetuning_beginner.htm
- http://www.redrc.net/2007/01/team-associated-launch-rc8-first-pictures/
- http://www.rchobby.co.uk/radio_controlled_cars.html
- http://www.rc-airplane-world.com/model-airplane-engines.html
- http://www.easyrc.com/index.html
- http://www.easyrc.com/cars-trucks/carstrucks4.html
- IIT Bombay, Techfest 08, FTGP tutorial.
The successful completion of this project is a glittering hallmark of academic achievement and I am greatly indebted to scores of individuals who have contributed their mite for the jubilant finish of this project work. I would like to express my sincere thanks to the following people, who in one way or the other helped or inspired me in the success of this project.
Mr.Murarie kumar, Mentor, guide and sponsor of this project
Dr. P.V.Mohanram, Head of Department of Mechanical Engineering
Mr. B.Giriraj, Faculty, Department of Mechanical Engineering
Sowrirajan K, Team member
Rakesh Narayanan, Team member
Ramani S, Team member
Ragunathaprabhu S, Team member
About The Author
Srihari.B
Founder : Team RHTP
Webpage:- http://rhtp.in
email id:- teamrhtp@rhtp.in
Labels: feature